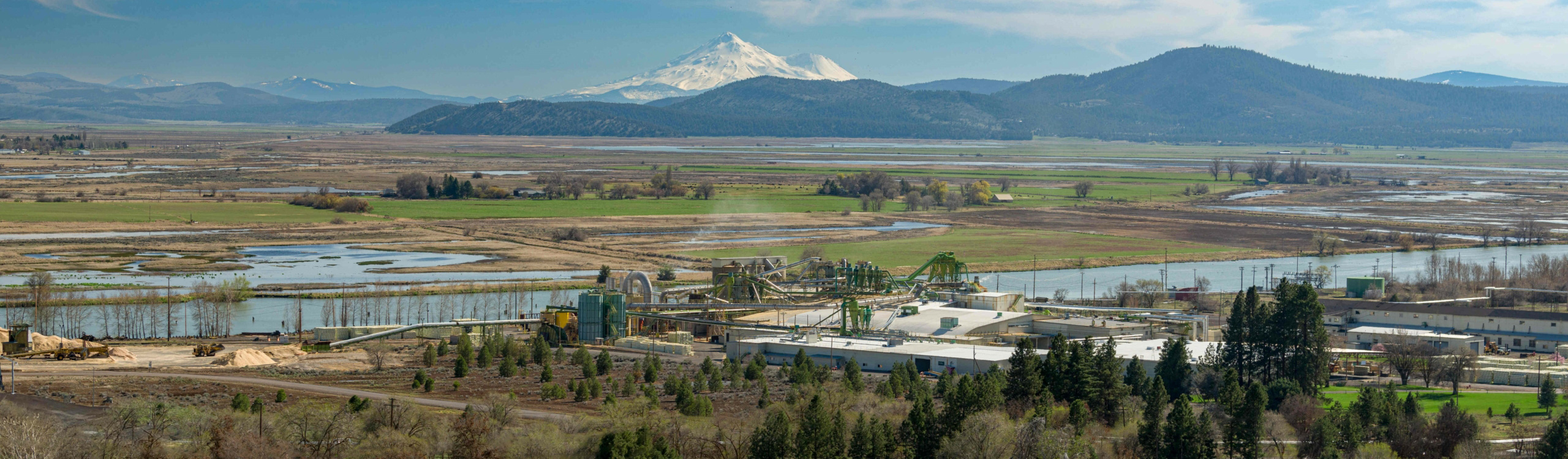
Take a walk through our step-by-step manufacturing process, starting with harvesting wood fiber sourced from dead trees, and ending with delivery of the final product.
1
2
3
4
5
6
7
8
9
10
11
12
13
14
15
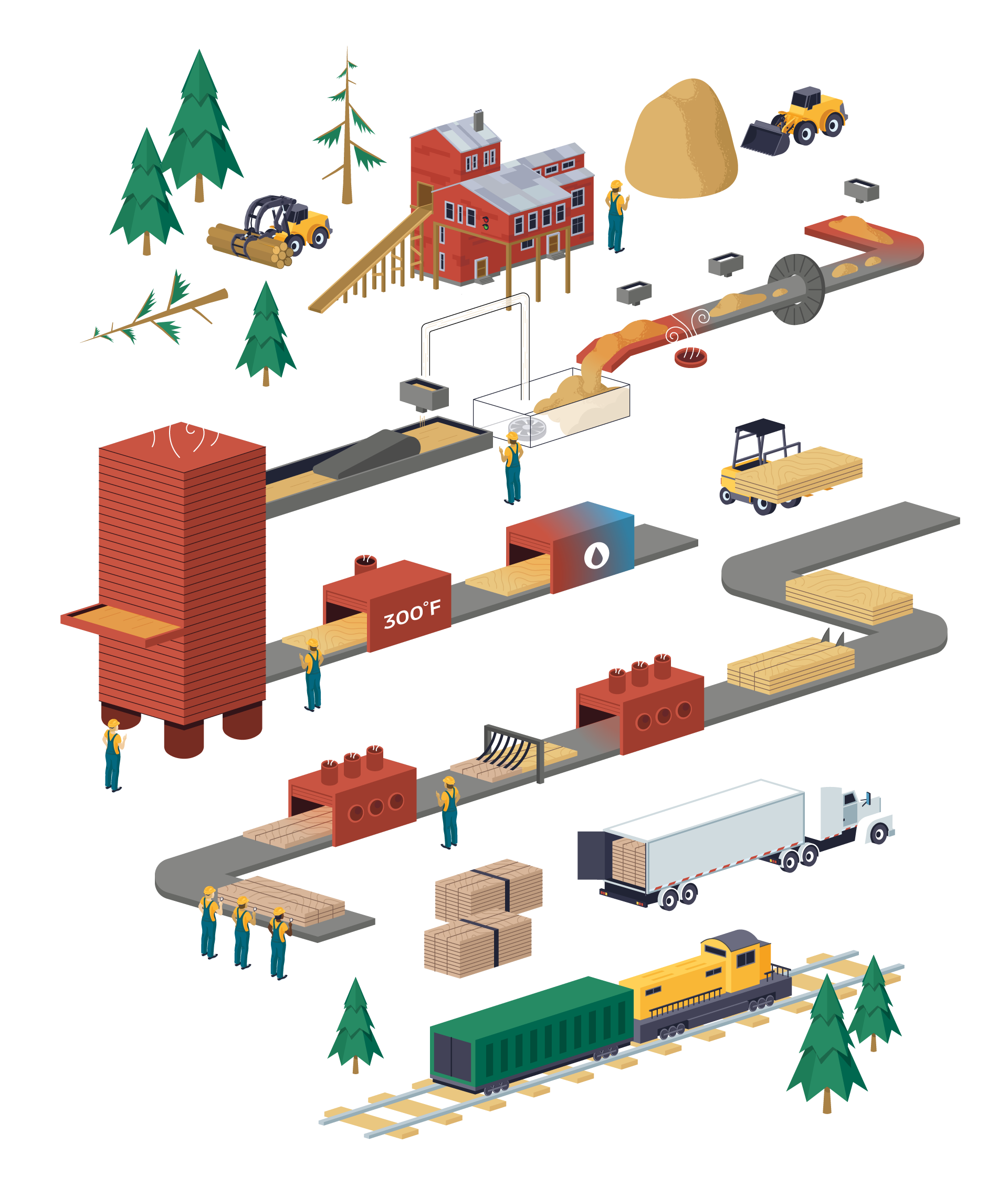
Take a walk through our step-by-step manufacturing process, starting with harvesting wood fiber sourced from dead trees, and ending with delivery of the final product.
STEP 1
Wood fiber utilized in producing TruWood® Siding | Trim is either a byproduct of other operations, or is manufactured from dead trees removed from the forest. Removing this leftover wood from forestland contributes to the overall vitality of the forest.
STEP 2
TruWood® utilizes wood residuals from our sawmill to prevent waste. Our Quality Control Team inspects the quality of the incoming raw material/wood chips.
STEP 3
The incoming wood chips are preheated with steam, and wax is added. After the preheater, the chips/wax are refined into wood fiber.
STEP 4
Resin is added to the refined fiber before entering the fiber drying system. After drying, zinc borate is added. Then the product goes into 2 fiber use bins.
STEP 5
The fiber is metered out of the use bins and into the forming heads. 5 layers of fiber form the fiber mat. The Quality Control Team will measure basis weight, moisture content, and proper additive addition.
STEP 6
After the mat is formed, the pre-press squeezes out all the air and consolidates the fiber mat. The mat is conveyed towards the hot press and cut into individual 4’ x 16’ sized mats. The mats are placed on caul plates into the press loader.
STEP 7
Each caul plate/mat is assembled in the press loader. The hot press then loads and presses 30 mats into master panels. Inside the hot press, chrome-plated press plates provide the distinctive textures of TruWood® Siding | Trim (Old Mill, Shake, Adobe, etc.). The Quality Control Team measures for proper density, pressed caliper, length, width, square, internal bond, modulus of rupture, etc.
STEP 8
The 4’ x 16’ master panel (various textures) has the sides and ends trimmed. The Quality Control Team checks for proper dimensions, length, width, and caliper. The mats are loaded into racks, to be placed in the bake oven for full cure.
STEP 9
The baked racks go into the humidifier for cooling and proper added humidity.
STEP 10
Master panels are run through a saw system and cut to proper width and length (trim, lap siding, and panel siding). Edge machining for lap products is also done before any priming (drip edge, Sure Lock ™ edges).
STEP 11
The fully machined trim/siding is sent to the preheat oven, where high temperatures ensure consistent temperature before priming. Consistent temperature ensures that the primer adheres and cures properly on the product.
STEP 12
TruWood® Siding | Trim goes into a flood coater and a consistent dry film thickness is applied. The Quality Control Team ensures the proper dry film thickness (primer application thickness).
STEP 13
The primed siding/trim then goes into a final cure oven for complete drying and cure.
STEP 14
The Quality Control Team inspects for correct dimensions, ensures there is no curve, and the product is square. They verify excellent primer application and add a barcode.
STEP 15
TruWood® Siding | Trim is bundled, strapped, and loaded onto a semi-truck or a rail car.
Start your next order with our sales team.
Contact a TruWood® sales rep and find your Tru Fit!